-한국기계연구원 열에너지솔루션연구실 2028년까지 6년 과제로 선행기술 개발
-사이클 설계 및 압축기, 열교환기 등 시스템 요소기술 개발
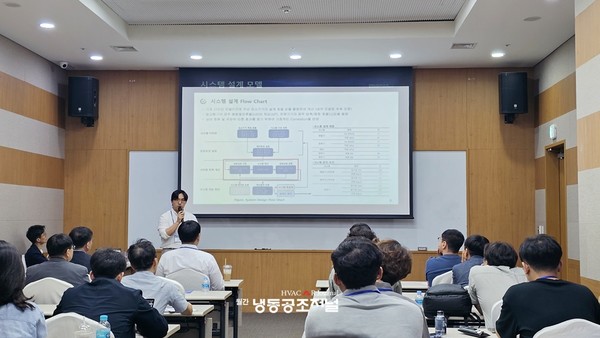
산업용 고온 히트펌프는 산업배열을 재활용해 고온의 열에너지를 생산하는 고효율 장치로서, 기존의 화석연료 연소 보일러를 대체하고 탄소중립을 달성할 수단으로 각광받고 있다.
하지만 현재까지 상용화된 고온 히트펌프의 열공급 온도는 200°C 미만이며 산업 열공정 수요의 상당 부분을 차지하는 300°C 이상의 열공급을 위한 히트펌프는 요소기기 개발 및 냉매 선정 등 기술개발의 특성과 난도로 인해 연구개발이 미비한 실정이다.
한국기계연구원 열에너지솔루션연구실(실장 송찬호)은 2023년부터 2028년까지 6년 과제로 화석연료에 의존하고 있는 산업공정 열에너지의 탈탄소화를 위한 300℃급 고온 히트펌프 선행기술 연구개발을 진행하고 있다.
한국기계연구원은 6월 22일 용평리조트에서 열린 대한설비공학회 2023년 하계학술발표대회에서 선행기술 연구개발과 관련해 △300℃급 고온 히트펌프 시스템의 사이클 성능 해석 연구(정융 한국기계연구원) △300℃급 고온 히트펌프용 열교환기 설계기술 개발(김진섭 한국기계연구원) △고온 히트펌프 시스템용 압축기 개발(서정민 한국기계연구원) △역브레이튼 사이클 고온 히트펌프 설계 파라미터 해석(김진서 인하대 기계공학과) △300℃ 이상의 고온에 노출된 시멘트 복합재료의 열특성 실험 연구(김성곤 군산대)의 논문을 발표했다.
정융 한국기계연구원 연구원은 ‘300℃급 고온 히트펌프 시스템의 사이클 성능 해석 연구’ 발표에서 “정부의 2050년 탄소중립(Net-Zero) 실현을 위해서는 국내 에너지 소비의 62%를 차지하는 산업공정 열에너지의 소비 감축은 필수적이다.”라며 “산업용 고온 히트펌프는 산업배열을 재활용해 고온의 열에너지를 생산하는 고효율 장치로서, 기존의 화석연료 연소 보일러를 대체하고 탄소중립을 달성할 수단으로 각광받고 있다.”고 말했다.
하지만 현재까지 상용화된 고온 히트펌프의 열공급 온도는 200°C 미만이며 산업 열공정 수요의 상당 부분을 차지하는 300°C 이상의 열 공급을 위한 히트펌프는 요소기기 개발 및 냉매 선정 등 기술개발의 특성과 난도로 인해 연구개발조차 미비한 상태이다.
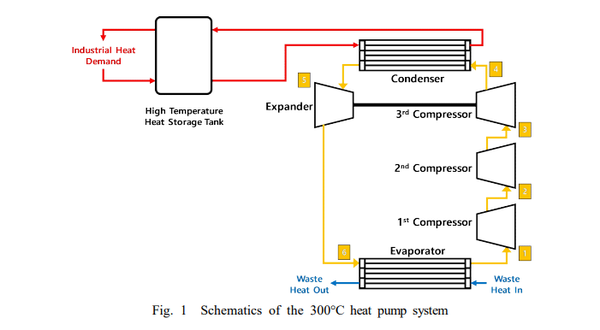
기존의 히트펌프와 같이 이상유체가 이상 영역에서 증발 및 응축을 통해 열에너지를 전달하는 방식에 대응할 수 있는 합성 냉매를 300°C 이상의 온도 대역에서는 찾기 어려워 자연냉매를 활용해 기상영역에서 작동하는 역-브레이튼 사이클 (Reverse Brayton Cycle) 방식으로 시스템을 구축해야 한다 또한, 고온의 기상 냉매와 2차유체를 활용하기 때문에, 이에 맞는 열교환기와 유체기기의 개발도 필요하다.
정융 연구원은 “이번 연구에서 자연냉매 기반의 역 브레이튼 사이클을 활용한 300°C급 고온 히트펌프의 사이클 계산을 통해 열교환기 효율에 따른 시스템 COP맵을 확인했다.”라며 “열교환기 차압은 각각 30kPa과 80kPa 미만, 총합 열관류율을 11kW/K 이상으로 설계해야 한다.”고 제시했다.
이어 정 연구원은 “앞으로 압축기 및 팽창기의 효율에 따른 COP맵 변화를 확인하고, 재생기 사이클과 다단 기상주입 사이클 등 응용 사이클에 대한 고찰을 수행해 최종적으로 300°C급 고온 히트펌프의 실험 및 실증 설계에 대한 최적화를 수행할 것이다.”라고 밝혔다.
김진섭 한국기계연구원 연구원은 ‘300℃급 고온 히트펌프용 열교환기 설계기술 개발’ 발표에서 “국내 산업공정에서 사용되는 열에너지의 90% 이상이 석유, 석탄, LNG와 같은 화석연료로부터 공급되고 있어 산업공정 열에너지의 전기화가 무엇보다 시급한 과제로 인식되고 있다.”라며 “기존 히트펌프에 사용하는 냉매의 임계 온도 한계와 압축기 오일 열화 등의 문제를 극복하고 고온 히트펌프의 최고 온도를 300℃ 수준까지 상승시키기 위해 기체 상태의 자연 냉매(공기)를 사용하고 역브레이튼사이클(Reverse Brayton cycle)을 활용하는 새로운 고온 히트펌프 시스템 개발이 필요하다.”고 말했다.
김 연구원은 이번 연구에서 300℃급 고온 히트펌프 시스템 개발을 위해 고온부 열교환기 설계 사양에 맞도록 핀튜브 열교환기와 판형 열교환기를 선정하고, 각각의 주요 설계 변수의 영향을 검토했다고 소개했다.
두 열교환기의 핵심 설계변수의 변화에 따라 압력손실, 2차 측 출구온도, 그리고 전체 체적에 미치는 영향을 분석한 결과, 핀튜브 열교환기의 내경이 20mm 부근에서 가장 높은 열교환 효율을 나타냈으며, 이때 1차 측 압력손실은 10.1kPa로 산출됐다. 또 판형 열교환기의 plate 수를 증가시킬수록 압력손실은 감소하고 열교환 효율도 증가하지만, 전체 열교환기 체적은 증가하게 된다.
김진섭 연구원은 “plate 수가 240개일 때(높이 ~ 723 mm), 1차 측(18.2 kPa)과 2차 측(47.9 kPa) 모두 압력손실 사양을 만족하는 것을 확인했다.”고 언급했다.
서정민 한국기계연구원 연구원은 ‘고온 히트펌프 시스템용 압축기 개발’ 발표에서 “공기를 작동유체로 사용해 300℃급 고온의 열을 공급할 수 있는 히트펌프에 적용될 압축기 사양 설정 및 개념 설계를 통해 히트펌프 시스템을 구성하는 터빈과 압축기를 구동할 전동기를 고려해 구성 설계를 진행한 후 비속도 분석을 통해 적정 회전수와 목표 효율을 결정했다.”고 밝혔다.
이번 연구에서 압축기는 300℃급 고온 히트펌프 시스템을 위해 3단으로 구성했다. 특히 작동 유체의 온도가 가장 고온인 3단 압축기는 전동기를 적용하지 않는 터빈과 back-to-back 구조를 채택해 고온의 작동 조건에 따른 전동기 냉각 문제를 발생하지 않도록 했다.
서 연구원은 “압축기 3단은 터빈과 back-to-back 구조를 고려해, 축동력 78kW, 회전수 50,000rpm을 가지며 비속도 0.717로 예상되는 효율은 약 81%이며 또 압축기 1단 및 2단은 동일한 사양의 전동기로 구동해 회전수 50,000rpm일 경우 축동력이 각각 104kW, 102kW이고, 비속도가 각각 0.842, 0.690로 이 경우 예상되는 효율은 각각 약 81%와 80%이다.”라고 말했다.
이어 “이번 연구에서 도출된 300℃급 고온 히트펌프용 압축기 목표 설계 사양을 바탕으로 향후 기본 설계, 상세 설계 및 성능 해석의 과정을 거쳐 압축기 공력 설계를 수행할 예정이다.”라고 언급했다.
김진서 인하대 기계공학과 박사과정은 ‘역브레이튼 사이클 고온 히트펌프 설계 파라미터 해석’ 발표에서 산업열 공급을 목적으로 기본적인 형태의 역브레이튼 히트펌프 사이클과 재생열교환기를 추가한 재생히트펌프 사이클을 구성해 성능해석을 수행하고 구성부의 주요 설계 파라미터에 대해서 성능 변화를 분석한 결과를 소개했다.
김진서 박사과정은 “이번 연구에서 고온 열 공급을 위한 단순 및 재생히트펌프 사이클에서 주요 구성부의 설계파라미터에 따른 성능계수 변화를 확인했다.”라며 “재생히트펌프 사이클이 단순히트펌프 사이클 대비 동일한 압축기 출구온도 조건에서 높은 성능계수를 나타냈다.”고 말했다.
이어 “히트펌프를 구성하는 압축기 터빈 열교환기의 효율 증가는 성능계수를 증가시킨다.”라며 “단순 히트펌프 사이클에서는 압축기보다는 터빈 효율 변화가 큰 영향을 주고 재생히트펌프 사이클에서는 재생열교환기로 인해 터빈 입구온도가 낮아지기 때문에 터빈의 출력이 작아 터빈 효율 변화가 시스템 소모 동력에 미치는 영향이 줄어들어 단순히트펌프 사이클에 비해서 성능계수에 영향이 작아진다.”고 밝혔다.
김성곤 군산대 토목공학과 박사과정은 ‘300℃ 이상의 고온에 노출된 시멘트 복합재료의 열특성 실험 연구’ 발표에서 “보통 포틀랜드시멘트를 활용한 시멘트 복합재료에 그라파이트를 각각 0 및 15% 치환해 혼입량에 따른 고온에서의 열특성을 평가를 통해 그라파이트 치환율과 열사이클 적용 횟수에 따른 단위중량과 열전도도 변화를 분석한 결과 그라파이트 치환율이 0%에서 15%로 증가할수록 열전도도는 54.83% 증가했다.”라며 “시멘트 복합재료에 적절한 양의 그라파이트를 치환해 사용할 경우, 열에너지 저장 성능에 긍정적인 역할을 기대할 수 있다.”고 언급했다.